Introduction to Six Sigma
Streamline Success: Master the Six Sigma Pathway
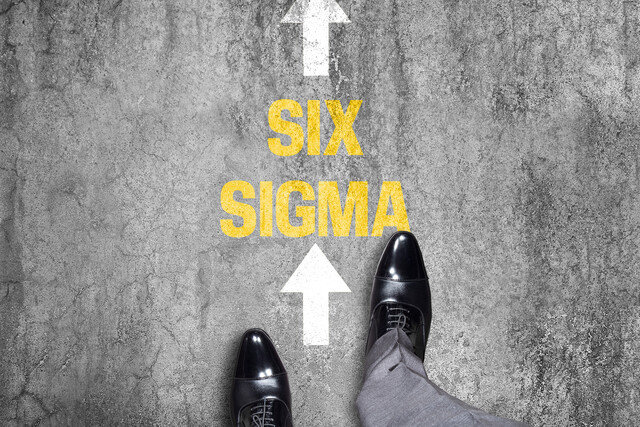
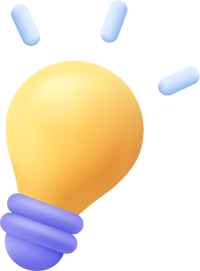
9 Hours average completion time
0.9 CEUs
15 Lessons
34 Exams & Assignments
55 Discussions
15 Videos
16 Reference Files
Mobile Friendly
Last Updated February 2024
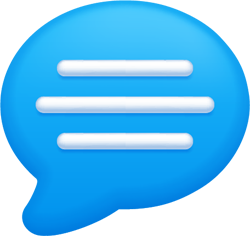
Mastery of Six Sigma Principles
Six Sigma stands tall as a robust methodology, central to ensuring projects achieve their pinnacle of success. Rooted in principles that champion excellence, Six Sigma is built on a rich tapestry of time-tested best business practices. The ultimate aspiration of this approach? Crafting an operational milieu that is almost devoid of errors.
The intriguing moniker 'Six Sigma' derives from the Greek letter sigma, traditionally employed by mathematicians to gauge variability. Translating this to the business arena, variability becomes a yardstick for assessing errors within processes. Striving for perfection, Six Sigma aims to achieve an outstanding rate of fewer than 3.4 glitches for every million transactions, where a transaction can be visualized as a tangible product manufactured or a service executed.
The success story of Six Sigma lies in its evolutionary nature. By eliminating the redundancy inherent in preceding business methodologies, it has ascended to an esteemed pedestal, revered as a top-tier project management system. Prestigious global corporations vouch for Six Sigma's principles, driven by a contemporary business landscape where consumers are no longer content with mediocrity. They demand unparalleled excellence, compelling enterprises to raise their game in a market teeming with rivals.
Our course is a comprehensive tapestry, intricately weaving the core aspects of Six Sigma, designed to equip you with the knowledge and skills to don the prestigious mantle of a 'Black Belt'--an esteemed Six Sigma team player.
Detailed Course Outline
-
History of Six Sigma: Delve deep into the origins of this methodology. Understand how it has evolved over the years, drawing examples from pioneering companies that adopted and benefitted from it.
-
Implementing Six Sigma: Gain insights into the practical aspects of embedding Six Sigma principles into a business framework, spotlighting real-world success stories.
-
Becoming a Customer and Market-Driven Enterprise: Understand the pivotal role of customers. Learn strategies that pivot businesses around market demands, underpinned by illustrative case studies.
-
Customer Expectations and Needs: Dive into the psyche of the modern consumer. Decode their aspirations, needs, and expectations to tailor products and services that resonate.
-
Linking Six Sigma Projects to Strategies: Harness the power of strategic alignment. Explore how Six Sigma projects can be seamlessly integrated with overarching business strategies.
-
Attributes of Good Metrics: Metrics are the compass guiding businesses. Discover the characteristics of effective metrics that facilitate informed decision-making.
-
Using Resources Wisely: Master the art of resource optimization. Learn how to allocate and utilize resources efficiently, maximizing ROI.
-
Project Management Using the DMAIC and DMADV Models: Grasp these core Six Sigma models. Understand their nuances and applications, enriched by engaging case studies.
9-11. Define, Measure, and Analysis Phases: These modules dissect the first three phases of the DMAIC model. From defining problems to measuring metrics and analyzing data, understand the intricate steps that drive project success.
12-13. Analyzing Data Modules: Comprehend the art of data analysis. Whether it's streamlining value streams or experimenting with designs, these lessons emphasize data-driven decision-making.
14-15. Improve and Control Phases: The culmination of the DMAIC model. Learn how to implement improvements and establish controls to maintain those enhancements.
Why This Course?
Six Sigma, with its potent blend of analytics, strategies, and customer-centricity, is not just a methodology--it's a philosophy. In a world where competition is fierce, and customer loyalty is gold, embracing Six Sigma can be a game-changer.
Our course is not a mere academic exercise; it's a journey. A journey filled with insights, real-world examples, and hands-on exercises. By its conclusion, you'll not only comprehend the theoretical nuances of Six Sigma but be adept at applying them in real-world scenarios.
In a marketplace that rewards excellence, equip yourself with the tools to not just survive, but thrive. Dive into the world of Six Sigma with us, and chart a course to unparalleled professional success.
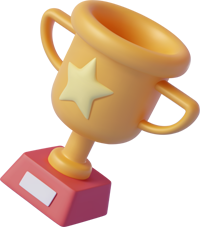
- Data-driven process improvement
- Effective project management
- Metric-based performance evaluation
- Resource optimization skills
- Customer-driven decision-making
- Error reduction techniques
- Strategic alignment of business initiatives
- Predictive data analysis
- Lean waste elimination methods
- Cross-functional team collaboration
- Continuous quality improvement
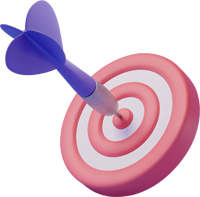
Choose from plans starting at just $16/month (billed annually)
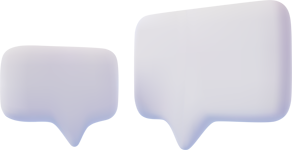
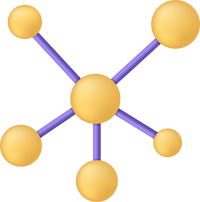
See Your Team Succeed
Empower your team instantly with an integrative group enrollment system. Purchase licenses in bulk with Group Discounts.
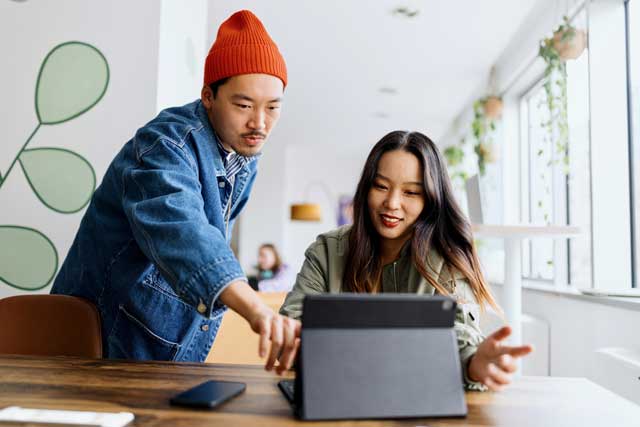
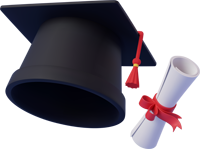
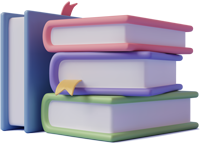
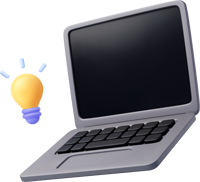