Key Definitions
1. Error-proofing � The process of using design or process features or qualities to prevent errors and their negative impacts on production. It is also called Poka Yoke, a Japanese word for "avoiding inadvertent errors".
2. Deployment chart � A comprehensive flowchart that indicates who performs which step in a process.
3. Continuous pressure hydraulics � This is the process of transmitting undiminished pressure in an enclosed stationary fluid.
4. Offset checks � These are method use to check and offset tool or equipment values to verify that they are within the recommended value.
5. Facilitation � This is the process of making it harder to commit an error and easier to do the right thing.
Most managers would probably be pleased if processes were followed or executed to the letter (99% of the time), but what does this mean? If work is done correctly 99% of the time, this equals to at least two unsafe landing in an international airport, six thousand pieces of lost email each hour, twenty-thousand incorrect drug treatment every year or five hundred incorrect surgical processes completed every week. In organizations, even the slightest of error, for instance, 0.009% can have a huge impact on a firm's financial profitability and performance.
Organizations errors are usually a result of miss-set workpieces, missed process steps, adjustment errors, faulty machine operation, bad tool or fixture preparation, or setup errors. Eliminating product defects via error-proofing yields business benefits such as better quality, better predictability of production output and quality, improved scrap rates, less redundant and rework inspection, reduced variability, and lower costs because the products will be produced correctly the first time.
Relationship Between Error-proofing and Lean Management
Error-proofing is an important element of lean management because it aims to eliminate or reduce defects. It impacts all areas of lean management, including processing, inventory, motion, correction, waiting, material movement and overproduction. In general, lean management and error-proofing both aim to reduce or eradicate all activities outside the ordinary value stream.
For instance, the outcomes of error-proofing can be seen clearly in the waste of overproduction. Producers may decide to overproduce a product because a certain percentage of waste is expected. Here, producers have introduced and accepted more ravage into the processes. Successful error-proofing can eradicate the need for overproduction through producing the product right the first time.
Guidelines to Error-Proofing Achievement
There are seven steps that organizations should follow to successfully implement error proofing. They are:
1. Quality processes � Managers should design robust and quality processes to eradicate all defects.
2. Utilize a team environment � Managers should leverage the team or employees' experience and knowledge to improve the error-proofing efforts.
3. Elimination of errors � Managers should use a robust crisis solving technique to drive defects or errors.
4. Managers should search and remove the root cause of the defects using the 2 Hs and 5 Why's approach.
5. Do it correctly the first time � Managers should use scarce resources to complete tasks correctly the first time.
6. Eradicate no value adding decisions � Managers should not make excuses � they should offer guidance.
7. Managers should implement an incremental continuous improvement process.
Error-Proofing Process
There are five main steps that can help managers implement total error-proofing. They are:
1. The first step is to develop a flowchart of the process involved. Every step should be reviewed in details and questions asked on when and where human errors can occur.
2. The second step involves working back via the process to find the source of the errors identified in step 1.
3. For every error, managers should find ways to make it unlikely for it to occur. For instance, consider:
-
Replacement � substituting the process with an error-free one.
-
Elimination � totally removing the process.
-
Facilitation � making the error harder to make than making the right action.
4. If managers cannot make it impossible for the defect or error to arise, they should look for ways to spot the error and minimize its consequences. Here, different methods can be implemented such as inspection methods, regulatory function and setting function.
Setting function is a method through which a product or process performance metric, or attribute is inspected for defects or errors. The following are the 4 type of function setting that managers use;
-
The grouping or fixed-value and counting method counts parts, repetitions or weighs a product to ensure it is complete.
-
The physical or contact method looks for physical characteristics such as temperature or diameter, frequently using a sensor.
-
The sequencing or motion-step method inspects the process sequence to ensure that steps are executed in order.
-
Another setting function is often added: information improvement. This ensures that information is always available and perceivable where and when required.
Regulatory function is a signal that alerts the employees that an error has arisen.
-
Warning functions are buzzers, lights, bells, as well as other sensory signals. They are often in the form of color-coding, distinctive sounds, symbols, and shapes.
-
Control functions which prevent the process from continuing until the error are resolved or condition is correct.
5. The last step is to choose the ideal error-proofing device or method for every error. The device should be tested before it is implemented. There are three types of inspection methods that offer quick feedback. They are:
-
Self-inspection � employees check or inspect their work after completion.
-
Successive inspection � done at the next stage of the process (by the next employee).
-
Source inspection � done before the process begins to ensure that the conditions are correct. It is often an automatic process and cannot continue to the next step until the product is right.
Illustration of Mistake Proofing
The following example shows a restaurant that wished to ensure quality service through mistake-proofing. The management reviewed the deployment chart of the seating process indicated in the figure below and identified human mistakes on the part of customers or restaurant staff that could lead to service issues.
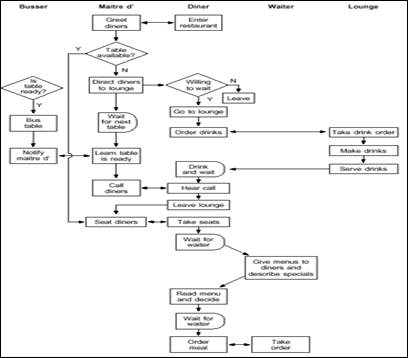
Figure 1: Restaurant's deployment chart
The first probable error occurs when a customer enter. The maitre d' may not realize that a customer is waiting if he/she is escorting another customer to his/her table, conferring with kitchen employee, or checking on table condition. Here, the error-proofing gadget is an electronic feeler on the entry door. The feeler sends a sign to a beeping pager on the maitre's pocket to ensure that he/she always knows when a person enters the restaurant.
A probable error on the customer's side is when the diner is announced when the customer is in the lounge � when his/her table is ready. The customer might miss the announcement if the lounge is noisy, if he/she is hard-of-hearing or if he/she is engrossed in a conversation. The error-proofing method selected by the management is to replace the ordinary process of announcing through a speaker by noting a unique visual sign of identifying the customer when the table is ready. For instance, the table busser signals the waiter, who approaches the maitre d' and find out how to identify the customer. The waiter gets the customer in the lounge, escorts him/her to his/her table, gives him/her menu and takes extra drinks orders.
Objective and Methods of Error-Proofing
The objective of error-proofing is to prevent a defect from arising and if it is not possible, to detect the defect whenever it occurs. There are different levels, effort, as well as costs of error-proofing. The management needs to identify the ideal levels and evaluate the feasibility of implementation. There are three types of error-proofing methods:
1. Sequence method � It determines if processes were followed.
2. Fixed-value � Determine if the specific number of movements were achieved.
3. Contact method � Spots defects through testing product quality or characteristics.
Defects found in final steps or operations of a process are more costly because they feature a higher percentage of overhead, material, labor than defects detected at the start of the production process. In addition, if a defective product reaches the consumer, the intangible assets, such as relationship and reputation, can easily exceed the visible costs and can ruin a company.
Note: GOOD methods detect the error before continuing to the next process, BETTER methods detect the error while in the process, and BEST methods prevent the error from arising at all.
Methods of Error-Proofing
Error-proofing consists of three methods: contact, counting, and motion-sequence. These methods can be implemented in warning or control systems. Every method uses a unique process of prevention approach to detect defects.
1. Contact methods
Contact methods do not need to be of high technology. Passive gadgets are often the best method. They can be as straightforward and simple as guide blocks or pins that do not allow material to be in the wrong place before processing. They take advantage of material designed with an unequal shape. Contact method signals to the employee right away that the material is not in the right place.
2. Counting methods
Counting methods are used when a specific number of operations are needed within a process when products have a fixed number of elements that are attached to them. Sensors count the number of times elements are used or processes are completed and release the product only when the set count is reached.
3. Motion-sequence Methods
These methods use sensors to determine if steps or motion in a process have completed or occurred. If the motion or steps have not occurred or have occurred out of schedule, the sensors signal timers or other gadgets to stop the machine and even alert the operator.
Fail-safe System and Error-proofing
Error-proofing is a 100% inspection at the source technique, rather than two or three steps down the process. In general, error-proofing enhances the predictability of output. Thus, the actual inspection duration, which is a typical nonvalue added activity in production processes, is lowered. Error proofing seeks to make sure that every process output is in the exact specifications given by the client.
The concept of error-proofing has a lot of applications in our daily life. For instance, childproof caps on tablet bottles prevent kids from opening them and taking harmful drugs. Shift/brake interlocks system in vehicles which prevent the vehicle from being started unless or until the clutch or brake is depressed. These two are example of fail-safe systems. They prevent the error from occurring, and they are normally used where the loss, in the event that the loss occurred, would be unbearable.
There are also many examples of error-proofing in the modern industry. For instance, barcode scanning at a supermarket or grocery store speeds up the verification process and eradicates errors caused by keying the wrong price. Another example is a torque limiter on assembly tool that deters a person from over-tightening a bolt.
Incorporating Error-proofing into Manufacturing Processes
There are a few error-proofing techniques specific to production processes that managers can implemented to error-proof production. They include machine monitoring methods, program simulation for crash averting, tool-setting automation, safe programming, and tool condition monitoring.
One error-proofing method commonly used in the automobile industry is the implementation of continuous pressure hydraulics. Continuous pressure hydraulics utilizes live hydraulics in a workstation to enhance the clamping process through maintaining the right clamp force for the specific job. The steady clamping pressure keeps parts from deflecting during production; all parts come out with equal surface tolerance, eradicating variability.
Another error made during the production process is miss-setting parts when putting them in a machine fixture. Often, this occurs if pieces of waste are blocking indicators, resulting in parts being incorrectly positioned. This leads to production of inconsistent parts. To avert this, the continuous pressure hydraulic system uses coolant flushing systems in the middle of the fixture that eliminates debris before they block the sensor.
Finally, continuous pressure hydraulic uses electronic cycles to control the fixture's clamping systems. This makes sure that consistent clamping pressure is applied to all parts, eradicating the risk of manual miss-setting.
Other error-proofing techniques include implementing guideposts to avert miss-loading of parts and using diagrams or silhouettes to ensure that employees know the right orientation of the parts when putting then on the fixture.
There are other error-proofing strategies that can be used in the programming process. For example, tool path validation software replicates tool paths, allowing the employee to inspect for tool collisions before machining the part. The software practically machines the part and signals the employee in case of any issue between the fixture and the tool or between the table and the spindle tool. This can be really useful when doing low-volume production, which needs a lot of first-time setups and programming.
Error-proofing Tools and Machines
Mistakes caused by incorrect tool data frequently occur in manufacturing process. To eliminate tool data mistakes, a Balluff Sensor is used to read the right data from every tool into the system controller instead of manual input. This is realized through a read/write chip implanted into every tool with data such as tool length, diameter, and life remaining. This reduces mistakes by automating the manual process of keying the tool data into the machine.
Offset checks are another error-proofing process that can be incorporated into programs parts. They use macro programs to check as well as offset tool value to determine if it is within the acceptable value. This offers an added safety precaution in case a wrong value was manually keyed into the system by an employee.
Locating or situating the pallet into the system tool is a common stage where errors arise. Often, a pallet is well-secured to the machine by clamps that use feelers to ensure it is well aligned. However, it is possible for debris and chips to interfere with it. If the pallet is not aligned properly, the fixture and other parts will also be misaligned leading to further machining mistakes.
When to Use Error-proofing
Error-proofing is used in the following situations:
-
When processes have been identified that are prone to human error, particularly in processes that depend on the employee's skill, experience, and attention.
-
When an insignificant error in the process causes a significant issue later in the process.
-
When the results of an error are dangerous or expensive.
Stop Errors Before They Occur
Although errors cannot be totally eradicated from an organization, fail-safe systems can be implemented to make sure that human errors do not translate into operation or production defects. Through implementing these systems in the tooling, fixture, machining and programming processes, mistakes can be easily identified and defective products removed from the system before they lead to bigger problems downstream. By error-proofing different processes, managers can reduce quality, improve quality, reduce cost and improve global competitiveness.