Key Definition
1. Ishakawa diagrams � Ishakawa diagram, also called cause and effect diagram or a fishbone diagram, is a visualization tool for classifying the probable causes of problems with the end goal of identify their root causes.
2. Andon � Andon is a Japanese word meaning a system of notifying management, maintenance as well as other employees of a process or quality problem.
3. Jidoka � A pillar of Toyota Production System which highlights the root causes of problems.
4. 5Whys � It is a simple but an effective analysis technique to get to the source or root of a problem.
Total productive maintenance, TPM, refers to a holistic approach to production equipment maintenance that endeavors to attain perfect production. In particular, TPM seeks to make sure the production process is:
-
Free from defects
-
Free from breakdowns
-
Free from small stops, or downtimes.
-
Also, it seeks to deliver safe working conditions � free from accidents.
TPM attains these goals by introducing systemized methods designed to enhance the human and mechanical aspect with the primary goal of optimizing efficiency of business equipment. It holds that maintenance of equipment should not be left to the maintenance department alone; it requires integrated, cross functional collaboration.
Many business still hold the traditional philosophy, "I run it, your work is to fix it," or "'we are the manufacturers, you are the maintenance people." The older the company is, the more hard wired this mindset is, and the harder it is to alter it. In lean organization, managers strive to cultivate a culture where operators become the asset owner. They place emphasis on routine maintenance and overall equipment effectiveness.
Operator (autonomous) maintenance is an essential pillar of TPM and it aims to;
-
Equip machine operators with the necessary skills to perform routine maintenance activities independently.
-
Develop in them a sense of ownership of the equipment they operate.
Operator maintenance focuses on tasks such as inspection, lubricating, cleaning, monitoring and other routine tasks that traditionally were the sole responsibility of the maintenance department.
TPM provides that most instances of equipment failure and breakdown can be prevented through inspection, checking for loose parts, proper lubrication, and cleaning of production equipment. This is a paradigm shift from the traditional belief that proper maintenance is difficult than this. TPM provides that if machine operators spend just a few hours each day on these tasks, huge wins are realized. These include;
-
Less disruption in the production process.
-
Elimination of defects very early in the process
-
Development of a sense of equipment ownership by the operators.
TPM Pillars
First used in the mid-50s, TPM is a program for enhancing efficiency of production equipment and business processes in general. It's based on eight pillars and the 5S as the foundation.
TPM � It's 5S Foundation
5s is the foundation on which lean TPM system is based, because without it, TPM would collapse under the weight associated with indiscipline, disorganization and inefficiency. 5S supports total productivity maintenance because it creates a work environment that is clean, organized and self-maintaining. In particular, the 5s delivers the following benefits:
5s sets the pace for implementation of TPM and must be 100% mature prior to any attempt to any aspect of total productive maintenance. It's good to remember that even on its own, 5S is highly effective in improve a company's bottom line. It has been shown to deliver benefits such as increased productivity and quality. For instance, if the work station is visually organized and clean, time needed for maintenance are easily accessible � this has a favorable effect on equipment uptime.
The 8 Pillars
TPM has 8 pillars that are designed to boost reliability of production machines. However, it is important to note that human aspect is at the center of this TPM and employees must be continuously trained on how to identify and eradicate the 8 types of waste identified in lean management.
TPM is a program based on a defined structure and principles, and it should not be implemented as a set of techniques or tools to be adopted haphazardly.
1. Autonomous Maintenance � Also called Jishu Hozen
This first pillar in TPM, Autonomous maintenance seeks to place the role of basic business equipment and process maintenance on tactical staff (machine operators). This gives the maintenance staff more time to handle complex maintenance duties. The specific tasks that autonomous maintenance seeks to delegate to operational staff include:
-
Lubricating
-
Oiling
-
Tightening nuts & bolts
-
Cleaning machines
-
Inspecting for possible problems, and
-
Other actions required to boost productivity an useful life of the machines.
By being responsible for these simple maintenance tasks, operators develop a sense of owning the equipment, and downtime is reduced since the no time wasted waiting for maintenance staff to come and correct routine deviations that occur frequently.
On the other hand, maintenance staff is left with sufficient time to timely and fully address problems that require high technical ability, for instance, servicing and/or replacement of part. They are also able to schedule and perform planned tasks meaning production is cautioned from unnecessary interruptions.
Operators' maintenance benefits both the employees and the business in the following ways;
-
The tactical employees become more concerned about the efficiency and conditions of the machines they use.
-
Skills level of operation level employees increase as they develop a general understanding of the machines they use; this is the very multi-skilling objective that lean management aims to achieve.
-
Machines run at their optimal capacity because daily maintenance such as lubrication and maintenance is performed.
-
Technical issues, such as loose parts, are identified and rectified well before the machines goes out of operation.
-
The engineering department is freed-up to perform specialized maintenance on critical machines and aspects of the production processes, thus, decreasing the overall process downtime.
NB, by properly performing all the tasks outlined in this total productive pillar, capital investment is significantly reduced since the business does not need to repair machines on a regular basis. This is because forced depreciation is monitored through routine maintenance.
Pillar |
Explanation |
The Business Benefits it Gives |
Autonomous maintenance |
Provides that machine operators should be trained to complete routine maintenance tasks such as inspection, cleaning and lubrication of machines. |
� Boosts operators' knowledge of equipment. � Gives maintenance staff adequate time to perform critical tasks such as preventative maintenance � Gives operators a sense that they own the machines they run. � Facilitate early identification of problems, before they cause breakdowns. � Makes sure machines are properly lubricated, increasing their useful life. |
2: Planned Maintenance
This pillar provides that machine maintenance should be scheduled based on features of machines for example, breakdowns and failure rates. By planning maintenances in line with these metrics, the rate of failure and breakdown of machines is reduced, increasing the useful life of equipment.
Scheduling also helps to reduce disruptions to the production process, because equipment maintenance is moved to a time when machines are idle or producing too little. In fact, it makes it possible for the production department to build up temporary inventory; they get prior alerts of when maintenance is scheduled.
This is not possible in case of reactive maintenance which is delayed until problems arise resulting in negative effect on both machine downtime and productivity. In such cases, production managers cannot know when operation will resume, and more time is wasted since maintenance staff is usually lost in troubleshooting the possible cause of breakdown.
The following are the exact business benefits of scheduled maintenance over reactive maintenance;
-
By consistently scheduling maintenance, breakdown slowly decrease which in turn boosts capacity for productive tasks.
-
The production department can better plan its work since managers can tell the exact time that maintenance tasks will take.
-
Maintenance is matched to times when production work stations are not or least busy.
-
Capital investment is minimized as machines can be utilized to their full capacity.
-
Expensive replacement parts do not need to be held in inventory; they can be bought just prior to the planned maintenance time.
3: Quality Maintenance
Quality maintenance seeks to boost the capacity of production machines and processes are able to detect and flag errors during production, thus, boosting their capacity to manufacture to the right specifications. It also helps in identification and elimination of defects early in the production process, which would otherwise move down the value chain, resulting in more waste.
Using lean tools, for instance, andon and autonomation (jidoka), quality maintenance builds the capacity of machines to detect and flag abnormal conditions, thus, freeing operators form the repetitive and highly monotonous task of monitoring that is typical in non-lean businesses.
The quality maintenance pillar also builds in the workforce capacity of narrowing down to the root of deviations, instead of moving to solutions that are only short-term. This is attained through lean tools like Ishakawa diagrams and 5Whys root-cause analysis which is tested techniques of narrowing down to the actual reasons of deviation in the production process.
The business benefits of quality maintenance are;
-
It helps develop permanent countermeasures (inform of targeted improvements) to quality issues that recur in the production process.
-
Defects are reduced or fully eradicated.
-
The cost associated with producing sub-standard goods is eliminated by increasing the chance of manufacturing the product right the first time. This is because quality maintenance boosts capacity to identify and flag errors very early in the production process, minimizing the amount of reworks that might be needed.
4: Kobetsu Kaizen - Focused Improvement
This pillar requires managers to form cross-functional teams to examine problematic equipment and develop improvement strategies. The idea behind putting together a cross functional team is to have a diverse and large enough number of employees to bring varied viewpoints on the table.
Such teams are well-positioned to develop appropriate solutions to performance issues surrounding crucial machines. They also serve as training ground for workers on issues of total productive maintenance techniques and tools.
Once the improvement team is constituted, it selects one piece of equipment on a pilot basis and identifies all problems related to the equipment and the production process in which it is used. The team then holds a 3-5 days, in-house kaizen event to develop improvement strategies. In the event, participants map the current conditions as the baseline performance, against which they will evaluate future performance gains.
The cross-functional team works hand in hand to ensure that the solutions they agree on are implemented and follow-up activities are done within the specified timelines.
Therefore, focused improvement is beneficial since quick gains are realized that help promote lean management to workers who may be yet to buy in to the program. Also, it enables a business to equip a large number with expertise to use various tools for diagnosing machine and process deviations, and getting to the actual cause of the problem.
5. Early Equipment Maintenance
The fifth pillar in TPM, this pillar requires managers to use the knowledge acquired from past maintenance improvement task to make sure new equipment reaches optimal performance earlier than usual. It requires management to work closely with various stakeholders (especially supplier of equipment), to enable it to hit the ground running with productive and reliable machinery. For instance, given the information management has gathered during past maintenance, suppliers can be able to enhance operability and maintainability of the next iteration of machines. Such an approach dramatically reduces maintenance costs, improving the overall profitability of the business. Early equipment maintenance guarantees high productivity and output quality from the equipment right from the first day the machines are commissioned.
Some of the factors that management should advice suppliers to consider when outsourcing new machines include:
-
Ease of inspection and cleaning
-
Accessibility of various parts.
-
Ease of lubrication
-
Improved maintainability and operability of production equipment by placing key controls in such a manner that they are easy and comfortable to access and use to operators.
-
Facilitating changeovers through elimination of waste unnecessary steps and/or simplification of procedures.
-
Enhanced workplace safety.
-
Feedback mechanisms that helps combat out-of-specification situations, as well as giving clear indications of the appropriate specs.
It is good for lean mangers to note that although machines may be manufactured with the above factors in mind, it is possible that there will be problems that might need to be rectified prior to full commissioning.
Early management addresses these concerns and by using information from operators before installation.
6. Education and Training
Education and training, the 6th pillar in TPM, is concerned with bridging the gap that develops in a business after moving to total productive maintenance. It is states that lack of proper knowledge can stand in the way of TPM maintenance and cause mediocre and/or failure. Therefore, training is required to help employees understand lean tools such as TPM. Training the workers gives the organization reliable and knowledgeable employees who can competently lead the lean initiative.
The education and training pillar applies organization-wide. It requires managers to train all workers. It provides that all workers, from machine operators to the senior level management � are involved in TPM and must be trained.
7: Health, Safety & Environment
This pillar seeks to ensure that the working environment is safe, and free from all elements that can harm the workers well-being. It provides that although the primary objective of a lean organization is to create and deliver value to the customer in the most efficient and productive way, it shouldn't be done in a manner that is injurious to the health and/or safety of the workers.
It emphasis that all TPM tools put in place should take into account the safety and well-being of the employees above all else.
If employees are provided with safe working conditions, their attitude towards the organization, their work to be specific, improves significantly, resulting in increased productivity and metrics. Also, fatalities and injuries reduce significantly when management puts active effort towards creating accident-free working conditions.
This TPM pillar requires the cross-functional TPM team to develop strategies to make work areas and the machines safe. Normally, they do this by adding safety features such as works standards, guards, protective equipment, and installing first-aid kits within the work stations. Improving safety of the machines enhances productivity of the workforce.
8. TPM in Office Functions
The last pillar in TPM seeks to improve the administrative functions so the entire business is speaking the same language. Since administrative department is largely a support department, helping them learn and apply lean management principles make it possible for them to offer efficient services to the key value generating processes.
In addition, training workers in all departments creates a pool of employees who understand the axioms of lean management, and who can quickly be called upon to help in its implementation. Also, it promotes a culture of horizontal cooperation over the silo mentality.
Application of TPM in the administrative function on its own delivers benefits such as enhanced efficiency and productivity in execution of supportive duties. For instance, the administrative department is able to reduce the time they take to process an order, then production materials will be available on the shop floor in time. In addition, if material suppliers always receive their money in good time, then they will be able to offer the services they have been engaged to offer conveniently.
OEE and the 6 Big Losses
OEE is an operation metric that seeks to identify the scheduled production time that is spent generating true value to the clients. OEE was developed to facilitate implementation of TPM initiatives by allowing accurate tracking of the progress made towards lean production (perfect production). It's broken down into the following;
-
100% OEE � Perfect Production
-
85% OEE � world class for discrete producers
-
60% OEE � typical for a number of discrete producers
-
40% OEE � uncommon for producers without lean and/or TPM programs.
OEE has 3 provisions which map one on one with the goals of TPM that we discussed at the beginning of this chapter.
OEE consists of three underlying components, each of which maps to one of the TPM goals set out at the beginning of this topic, and each of which takes into account a different type of productivity loss.
Overall Equipment Efficiency
Overall Equipment Efficiency refers to a best practice metric used to identify the proportion of scheduled production time that is actually used in value adding (productive) activities. A Score of 100% represent ideal manufacturing; the business is producing good parts at all times, with zero down time. In TPM, OEE is applied as both a baseline and benchmark.
-
Baseline � To track progress of effort put to eradicate waste in the production process.
-
Benchmark � To analyze performance of a specific machine to industry standards, different manufacturing shifts/runs on the same asset, or to similar machines in the organization.
OEE is made up of 3 components that map one on one to the primary objective of TPM that we outlined at the beginning of this article. Each component accounts for a particular form of waste;
Performance |
Slow cycles, small stops. |
This component accounts for performance loss. I.e., any factor that causes manufacturing to run at other except the maximum possible speed. |
Quality |
Defects � free |
Quality accounts for quality loss during the production process. It takes care of reworks and manufactured pieces that fail to meet the specified quality standards. E.g., Decreased yield on start-up and production rejects. |
Quantity |
Idea Production |
OEE incorporates all losses (performance loss, quality loss and availability loss). Therefore, it is an accurate measure of the actual productive time. |
From the table above, it clear that OEE is closely tied to the TPM objectives f No slow running (measured by performance), no small stops (accounted by Availability) and Zero-defects (measured by quality)
OEE Formulas
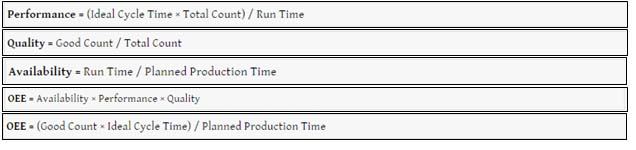
OEE helps in identification and quantification of productivity losses. It can also be used to measure and track the process gains arising from TPM implementation.
TPM Implementation
It is good to note that of all lean management tools, TPM is the hardest to implement because of 2 reasons;
-
Proper TPM implementation demands the highest culture change (compared to adopting other lean techniques and tools) from various functions within a company. The cultural change must be realized simultaneously.
-
Of all areas of possible lean management improvement in an organization, maintenance of equipment is usually the most neglected.
However, the benefits of proper TPM implementation far exceeds its cost � in terms of minimized scrap, on-time delivery, increased associate morale, and improved productivity. Probably, they are greater compared the once attained after implementing any of the other lean management tools and techniques discussed in this article.
Ideas for successfully implementing TPM
As we detail out the cultural change needed to support TPM implementation, it's good to revisit the 4 components of effective lean transformation. Lean management must be based on a foundation of strong lean culture.
The change towards a lean culture in an organization begins with establishment lean behavioral expectations. Lean expectations form the culture baseline. However, for successful TPM adoption, 2 additional cultural shifts must be realized;
-
Managers in most business consider the maintenance function a "necessary evil", or as undesirable "indirect" cost. As result, the maintenance function;
-
Feels comfortable when located the furthest from production and administrative department as possible.
-
Has little, if any regard for the manufacturing process.
-
Views themselves as mainly "on call".
-
Runs on chicken-wire repair or fire-fighting maintenance strategy.
-
Has no incentive to design preventive maintenance strategy.
This must be changed. In lean management, maintenance department plays a critical role in creating a world class company.
-
The second cultural change that must be cultivated is respect for the production process and machinery, tool, equipment and the output they produce. Often, businesses buy production equipment, are unconcerned about daily and preventive maintenance schedules. Later, operators start to complain that the business requires new machinery. More money is put into new equipment and the cycle goes on and on.
In addition, management must:
1. Make total productive maintenance a key part of the business culture.
2. Appreciate that developing a world-class TPM business takes time.