Key Definitions
1. Non-value-added activities � Refers to actions or activities that add no value to the final product or service, hence, a type of waste.
2. Value-added � Refers to actions or activities that add value to the final product or service.
3. Incident work � Activities required for the organization to legally stay in business.
4. Internal consumer � Receiver of final product or services inside the firm, typically the individual downstream process.
5. External receiver � Buyer of the final product; outside the firm (end consumer).
Lean manufacturing � Definition
Lean management is defined as a set of tools, principles, and production techniques that help in identification and elimination of waste through continuous improvements of the production process. Lean production principles endeavor to improve productivity, customer, and supplier relations to make sure the firm requires;
-
Less material
-
Less space
-
Less capital
-
Less human effort, and
-
Less time to manufacture products that precisely fits customer needs.
Lean management principles are based on the fact that every production process generates waste. Waste as used in lean manufacturing refers to non-value adding processes or activities such as;
-
Manufacturing more than the market demand.
-
Time in waiting.
-
Re-work.
-
Movement.
-
Misuse of materials, and
-
Unnecessary processing.
Lean production focuses on reducing or fully eliminating waste with the primary objectives of;
-
Improving productivity
-
Improving relationship to customers and suppliers
-
Enhancing flow.
Bear in mind that although lean principles originated from manufacturing firms, they apply equally to all types of business organization.
The Business Case for Lean Management
All businesses share a common goal � to produce more goods and services (at a standard or better quality) from the same amount or less input. Across the globe, this objective is becoming increasingly hard to attain, due to the rising cost of inputs such as labor, raw materials, capital, compliance and utilities costs.
These costs, coupled with a worsening dollar, are tightening profit margins. Consequently, the pressure to improve productivity and re-engineer business processes is back squarely on the list of priorities for most managers.
Adopting lean management can help a business enhance productivity and minimize cost by;
-
Reducing waste and eradicating non-value-adding activities.
-
Shifting your business model from push-focused to demand-focused.
-
Eliminating loss and deterioration of materials during processing.
-
Improving resource efficiency.
-
Delivering cost savings and elimination of waste through proper management of inventories.
-
Enhancing distribution of work.
-
Optimizing usage of machinery and physical space.
-
Reducing the amount of movement and information exchanges between processes.
According to NIST Manufacturing Extension Partnership, which recently surveyed 40 of their customers, applying lean manufacturing principles at the operational level of a manufacturing firm can, on average,
-
Reduce raw material costs by 8% to 16%.
-
Improve quality by 80%
-
Reduce manufacturing lead time by 90%.
-
Reduce space utilization by 75%
-
Increase productivity by 75%.
-
Besides these production gains, adopting lean manufacturing can help management improve business environmental sustainability performance.
Lean principles helps one analyze business processes with the view of eliminating unnecessary costs, improving inefficient processes, and reducing waste. It gives the following benefits:
-
Identification of problem areas and bottlenecks.
-
Simplifying processes
-
Saving money � minimizing expenditure on paperwork
-
Enhancing compliance with codes of conduct, rules, and regulations
Lean Management Principles - A brief History
Lean management principles began in production environments and are often described by a number of synonyms; Toyota production system, lean production, Lean manufacturing, and more. Most people mistakenly belief that lean manufacturing originated from Japan (Toyota production systems to be specific), but H. Ford was already using some sort of lean management as early as 1920. This is documented by the following statement,
"One of the biggest Ford accomplishments in reducing the price of our products is the continuous, gradual shortening of our production processes. The longer a product stays in the production process and the more it's moved about, the higher is its final costs." H. Ford, 1926.
Ford also used the concept of Continuous flow in the assembly line manufacture of Model T Cars. He kept quality standards extremely tight to ensure each production process fitted well into the next one. Therefore, H. Ford is credited as being the first person ever to use some principles of lean management.
But Ford processes were static. His assembly systems manufactured the same product over and over, and the system did not allow changes to the output or improvements to the processes. I.e., his model T assembly line could only produce model T vehicles. Ford's "Lean management" was also a push system where he determined the level of production, as opposed to the modern lean manufacturing where production is driven by market demand. The push system often resulted in accumulation of inventory (unsold items and W.I.P), ultimately resulting in high stock holding costs (wasted money).
Other businesses started to apply Ford ideas, but they soon realized that rigidity of Ford's system was a major hindrance to innovation. Later, Taiichi Ohno and kiichiro Toyota, built on Ford's ideas to develop what is now known as Toyota production system (TPS). Ohno used JIT (Just in Time Production) to enhance manufacturing efficiency. The system was later popularized by Womack, the author of the book titled, "Lean Thinking, The Machine that Changed the World and Lean Solutions."
Overview of Toyota Production System (TPS)
Lean Management Philosophy
The primary objective behind lean management is to "offer high quality products to more customers at the lowest cost possible, and to actively contribute towards building a more prosperous society." This philosophy is supported by a number of lean management principles that you must know for you to successfully implement and benefit from lean manufacturing. The following page reviews the more critical lean management principles to help you get started.
NB: Take these as the guiding principles of lean management since there are many more that we won't discuss. Typically, failure to understand and correctly apply any of the following lean production principles is the primary cause of lean implementation failure, or lack of support and commitment from everyone in the organization.
1. Define the External Receiver and Define Value;
When seeking to adopt lean manufacturing, the best starting point is to appreciate that only a small fraction of the total business time is transferred as value to the customer. Therefore, it is important to specifying exactly what constitutes value for a particular product, to facilitate identification and eradication of non-value added action and activities (waste).
The value principle requires everyone in the organization, from top management to shop floor workers, to understand the value that an external receiver places on the product. It's the perceived value that determines how much the customer is willing to pay for the product. Consequently, lean organization use a top-bottom target costing approach that is typical to lean manufacturers such as Toyota.
Top-bottom target costing determines prices of goods and services based on what the external receivers are willing to pay for particular features, services or products. It's the management duty to eradicate all types of waste from operational processes so that the price can be attained at the highest possible profit to the company.
2. Define and Map the Value Stream (VS);
The value stream refers to all the processes, actions, and activities within a firm that collectively deliver the final product. Once you have defined what constitutes value in the eyes of your customer, the next step is to determine how you are, or not, delivering the value to them.
3. Create Flow to Help You Eliminate Waste;
Generally, after mapping the value stream, you will realize that only 5 percent of business action and activities contribute value to the external receiver. This can increase to 45 percent in service businesses. Eradicating this waste makes sure that the final products "flows" to the external receiver without detour, interruptions or waiting. It guarantees the highest profit to the firm.
Types of Waste in Lean Management
Lean production categorizes waste into 8 basic types;
-
Waste of inventory
-
Waste of unnecessary motion
-
Waste of waiting
-
Waste of transportation
-
Waste of production of defective products
-
Waste of over-processing
-
Re-work
Each of these wastes (areas of inefficiency in an organization) is detailed in the following table;
Waste of Overproduction;
The corresponding lean management principle is to manufacture in adherence to a pull system, or manufacturing products or services just as the buyer orders them. Any item produced beyond market demand (safety stock, work in progress (WIP) inventories, buffer stock, etc) ties up material resource and valuable labor that would otherwise be utilized to respond to market demand. |
Waste of Inventory;
Closely related to overproduction, stocks beyond what is required to adequately meet market demand adversely affects cash flow, and occupies floor space unnecessarily. One of the most compelling benefits of adopting lean management principles is elimination of cost or postponement of plans to expand warehouses. |
Waste of Waiting;
Lean production requires production resources to be availed on a Just-in-Time basis; not too early, not too soon. |
Waste of Extra Processing; Refers to additional non-value steps such as;
Lean management principles require parts to be manufactured without burrs, using properly designed and well-maintained tooling, and statistical technique process control methods to minimize or eliminate the number of inspections required. VSM is normally applied to help in identification of non-value added processes; both in service and manufacturing firms. |
Material transportation/movement; (sorting, transportation, arranging items unnecessarily).
|
Motion; Unnecessary employee movement;
Unnecessary movement/motion is generated by poor workflow, housekeeping, undocumented or inconsistent work methods, and poor layout. Value stream mapping is again utilized to remedy this form of waste. |
Rework/Correction; Rectification of error;
Service errors and production defects waste resource in 4 major ways.
Lean principles require the product to be manufactured properly and correctly the first time. |
Underutilization of people;
|
NB* Normally, a mapping technique called Value-stream mapping is used to record the "Current state" of manufacturing processes, including both non-value added steps and value added steps. Value-stream mapping gives a high level view of the manufacturing processes as they are now. This information is then used by management to develop the "future state" processes after the organization has been leaned.
Although the above mentioned types of waste were originally derived from production environments, they can be applied to many different types of organization. The idea of waste elimination is to review all areas in your organization, determine where the non-value added work is, and reduce or eliminate it. The improvements mind-set must span across the organization.
4. Respond to Customer Demand (Pull);
This principle requires management to understand the market demand for their product, and develop effective and efficient production processes to help them meet this demand. The firm should only produce what the customer want, right when he or she needs it.
5. Pursue Perfection;
Creating perfect flow and pull begins with a well-thought reorganization of productions processes, but the gains become truly significant as all the processes add up together. The reorganization makes more and more piles of waste visible, and the process gradually gears up towards the theoretically perfect manufacturing end point.
A Typical/Tradition Organization VS a Leaned Organization
Concept |
Typical/Traditional Organizations |
Lean Organization |
People Utilization |
People must be busy during same work hours. |
Since production is in response to market demand, some people might not be busy. |
Inventory |
Views stock as an asset in line with generally accepted accounting principles (GAAPs). |
Views stock as a type of waste � It increases production lead-time and ties up capital. |
Batch size and ideal economic order quantity |
Very large � aim to process more to compensate for possible downtimes. |
One � consistent and continuous efforts are made to eliminate downtime. |
Work Groups |
Functional/traditional departments |
Cross functional groups/teams |
Work Scheduling |
Manufactures to meet forecasts |
Manufactures to meet actual demand |
Labor cost |
Mostly variable |
Generally fixed |
Accounting |
Based on the traditional FASB standards |
Through-put accounting. |
Lean management tries to rationalize production of goods and services by;
-
Eliminating waste at all stages of the production process
-
Building quality (value) into each process
-
Reducing costs � enhancing productivity
-
Developing integrated production techniques
-
Developing a unique approach to organization management
Guiding Principles of Lean Implementation:
The successful implementation of Lean Production can be achieved through adherence to five key principles:
1. For every product line, define what constitutes value from the point of view of the consumer.
2. Identify all value adding processes across the value stream for every product line, and eradicate all non-value adding steps.
3. Set up the value-adding processes such that they constitute a smooth flow.
4. Permit clients to pull value from upstream activities or processes.
5. Once value is defined, the value adding processes are identified, non-value-adding processes are eradicated, and process flow and pull are initiated. Repeat this process and encourage continuous flow toward the final goal of developing "perfect" value with zero waste.
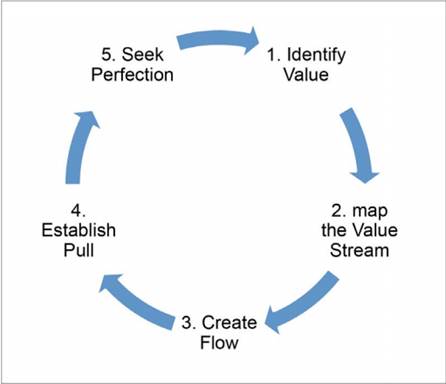
Kaizen (Continuous Improvement)
Kaizen, a Japanese word meaning change for better or gradual improvement, is arguably the most crucial element of lean management and for a good reason; without continuous improvement, the progress would stagnate. Kaizen provides that the change can be huge or small, but it must contribute toward better results. It holds that there is always room for improvement and therefore, the process of improvements is continuous.
A complete Kaizen cycle has 7 basic steps;
-
Standardize operations
-
Measure the standard operation
-
Evaluate measurement against goals
-
Innovate new methods and processes to achieve the desired output
-
Standardize the new operations.
NB* Do not get lost in only endeavoring to make the big changes; small improvements normally lead to big improvements, provided they are continuous and collective across the organization.