Key Definitions
1. Organization culture � This is a system of shared values, beliefs, and assumptions, which governs how individual behave in a company.
2. Human resource � They are people who comprise the workforce of a firm, economy, or business sector.
3. Brainstorming � A group creativity method by which efforts are put to find a solution for a certain problem by collecting a list of ideas spontaneously aired by its members.
4. Evaluation sheet � A document used to review employees' performance.
Introduction
Faced with massive competition and changing customer tastes, desires, and needs, organizations are adopting the Japanese kaizen to allow them to compete favorably, to meet customer needs, and to remain sufficiently flexible to respond swiftly to new challenges.
The simplest method for organizations to start adopting continuous improvement is to start thinking kaizen. In other words, organizations must adopt a mindset that facilitates continuous identification of Muda and continuous improvements to enhance productivity and efficiency of production processes.
Kaizen flourishes when it's embedded into the organization culture and in a cooperative work environment. In such organizations, kaizen becomes a means of improvement and it's represented in the daily struggles arising in the workstation and the way those struggles are resolved.
When a firm introduces a new process improvement tool or technique such as total quality management or quality circles, it gains some level of initial success. However, soon thereafter, such successes begin to wash away like fireworks on a summer night and management walks back to search for new ways to boost productivity.
This is because such organizations fail to adopt the first pillar of successful kaizen adoption � the kaizen mindset. In fact, without the right mindset, an organization cannot ensure continuous improvement. Developing the right kaizen mindset is the starting point of successful kaizen implementation; it creates the right perception of kaizen and a business environment that fosters commitment to a never ending endeavor for process improvement.
Elements of Kaizen Mindset:
1. Everything, no matter how good it is, can be improved � some Japanese managers go as far as to tell their employees to view the way they are currently doing their job as the worst way to do it.
2. Not a single day should pass without some form of improvement in the organization.
3. Do not criticize, suggest some ideas for improvement.
4. Kaizen requires everyone in the organization to challenge assumptions. Challenging assumption involves questioning the status quo. Olson Ken, the CEO of DEC, states, "The best assumption to hold is that the status quo and all commonly held beliefs are wrong."
Case study:
Albert Einstein is popular for making assumption and then asking searching questions to figure out their implications. For example, he assumed that he was riding on a sunbeam, moving around the earth at speed of light and then he tried to figure out how everything would appear to him. The final product of his enquiry was the General Theory of Relativity."
Challenging assumption is the beginning of creativity and identification of opportunities to reduce waste.
5. Think beyond common sense. Even if something is currently working well, look for opportunities to help you make it a lot better.
6. Ask searching questions � the creative process that opens the door for new ideas and improvement opportunities starts by asking yourself a lot of "What if?" and "Why?". For example:
o Why is X always manufactured this way? What if it's manufactured differently?
o Why do we view risk Y as a problem? Is there a way it can be changed into a competitive edge?
o Why do we focus on challenging the industry giant's market leadership position? What if we focus on penetrating a new market segment?
Also, ask other people in the organization to figure out what they don't like, how they would like it changed, and what else they would like to change.
7. Imagine the perfect customer experience and value and strive towards it.
8. Adopt customer-oriented strategies for improvement � all management activities should result in increased customer value and satisfaction.
9. Adopt a quality first mindset � not profit first. A business can only thrive if the consumers who purchase its products are happy with the services it provides.
10. Think about how it can be enhanced, not why it cannot be changed for better.
11. Establish a culture that emphasis on the processes � a culture that advocates for continuous process improvement � and management approach that rewards efforts for process-oriented improvement.
5 Strategies for Successful Implementation of Kaizen in an Organization
In an organization, a kaizen strategy is any process that works to continuously improve management and workers performance, process efficiency, value to customer, and collaboration between employees and management. Implementation of kaizen-oriented improvement processes requires some changes in your organization culture. Some of the most important aspects you should focus on to enhance adoption of Kaizen include:
1. Job satisfaction
For Kaizen to work, the workers must be pleased with their jobs and be committed to working towards improving their performance. The human resource team should conduct surveys to determine employees' attitudes and level of job satisfaction. Then, continuous efforts should be made to improve working conditions and employees' job satisfaction metrics.
2. Company involvement
The entire organization must be committed to Kaizen. The management needs to allocate time for workers evaluations, and workers need to be given time to monitor the management as well. The concept of Kaizen must be a priority.
3. Dedication
A Kaizen strategy needs to be presented to the management and the employees as a method of improving the organization productivity and to add to the firm's long-term goals. It might look like an ordinary approach to job development but its success depends on the employees and manager remaining dedicated. Implementing kaizen isn't easy, it requires dedication.
4. Teamwork
When an employee working with a Kaizen plan has a question about a process, he/she need to be encouraged to seek the answer from as many people as possible. Employees need to learn to function as a team and respect every staff's opinion.
5. Open-minded
The management and the employees need to have an open-mind for kaizen to work. Kaizen can be a significant change from the way people are accustomed to doing things, and the constant performance analysis can seem unrealistic and pointless at times. Therefore, management must encourage everyone in the organization to embrace kaizen, and to commit to making it a success.
Kaizen Approach Overview
The Kaizen approach demands that all workers participate; thus, everyone in the organization is encouraged to play a part in Kaizen implementation. As you will see from the diagram below, Kaizen has three key components:
1. Perceptiveness
All Kaizen activities are based on identified problems (wants/needs, function/timing/costs, and society/government/economy). There is no need of implementing it if there is no problem.
2. Idea development
This stage requires different people to participate in order to provide innovative ideas. The key is to form a Kaizen team to brainstorm possible solutions. The team should put together employees who work in the identified problem area, managers, and experts on kaizen adoption.
3. Decision, implementation, and outcome
Kaizen is only useful if and when it is adopted. The kaizen team should begin implementation of the identified solution, and routinely review its success.
The Kaizen Process in Practice
A step-by-step guide on how Kaizen can be used to implement in a meat tenderizer company:
1. Identify the problem/issue.
2. Form/create a team.
3. Gather/collect information from external and internal customer, and determine goals/objectives for the project.
4. Review the current process/situation.
5. Brainstorm and consider 7 possible alternatives.
6. Decide the 3 best alternatives of the 7.
7. Simulate and evaluate the 3 alternatives.
8. Present the suggestions and idea to the manager.
9. Physically implement the Kaizen outcomes.
10. Note the effects through evaluation.
Illustration:
This case study will focus on a kaizen project trying to improve operation in a meat tenderizer company. The full design of this organization is shown in the table below:
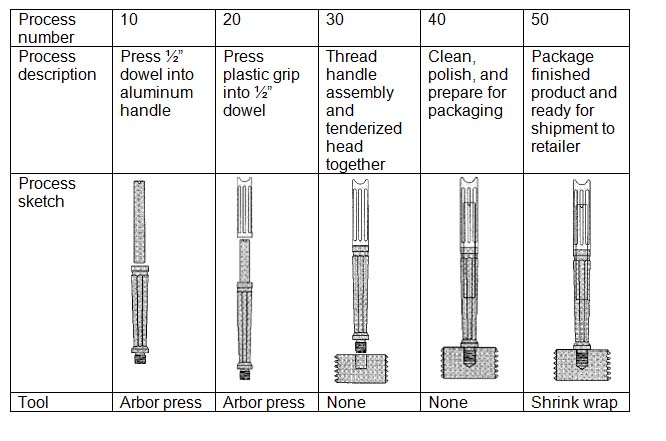
The problems identified in this process are:
-
The product is too expensive to produce.
-
The product is of low quality.
Therefore, there is the need to re-design the manufacturing system to improve the quality and reduce production costs. In order to do so, a manufacturing engineer, a design engineer, two machinery operators, and a quality engineer should be invited to the kaizen team.
After identifying the problem, creating the team, and discussing the problems with all the workers in that production station, the Kaizen team should meet to discuss the objective of the project. For this particular example, there objectives are identified:
-
Reduce 25 percent of the unit cost
-
Design a manufacturing system
-
Reduce the floor space by 15 percent
After setting these objectives, the Kaizen team can now begin to review the current situation/process of the product.
Once every person has fully understood the current system, a brainstorming session begins to generate ideas determining 7 new processes to be evaluated. All ideas are welcomed ranging from doing nothing to evaluating various methods to totally redesign the process. Seven is usually an ideal number because it generates a high degree of stimulation given the short-time assigned for the brainstorming session.
The 7 alternative methods should be displayed in a chart as shown below:
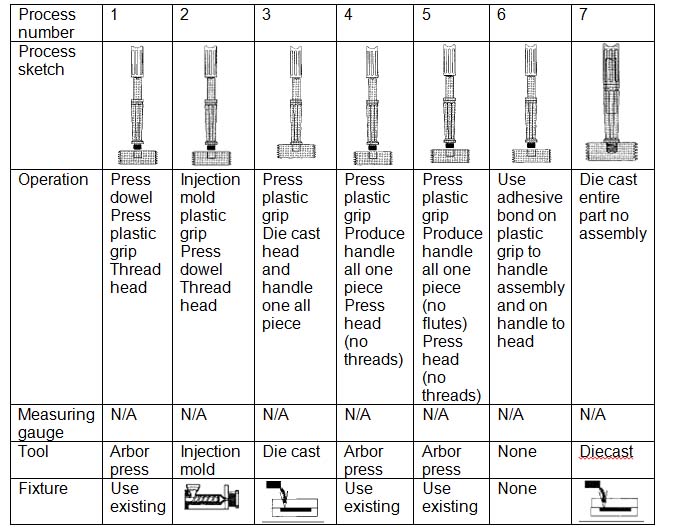
The group should then design an evaluation criteria based on the 3 objectives of the project. In our example, the criteria and the sub-criteria used are:
-
Flexibility � ease of repetition and simplicity
-
Cost � capital, tooling cost, labor cost, technology cost, maintenance cost, etc
-
Safety � safe, clean, desired quality, ergonomic, defects per shifts, required skills, customer specifications, etc
Assessing the Alternatives
The first column of the table that follows shows the evaluation criteria of the seven alternatives. Additionally, the weight of every criteria as well as the value of the sub-criteria's are determined and shown in the second and third columns respectively.
Here, an evaluation sheet is used to guide assessment of the 7 probable methods. The sheet should include categories that are suitable for the project. Once the sheet is ready, all members of the team should rate the 7 proposed methods on a scale of one to five.
One being the lowest, five the highest, and x for not applicable in this project. After all the members have rated the alternatives, the results are keyed into a chart and tallied. See the table below:
Proposed Methods |
||||||||||
Criteria |
Weight |
Value |
Sub-criteria |
1 |
2 |
3 |
4 |
5 |
6 |
7 |
Flexible |
25 |
5 |
Simplicity |
4 |
1 |
1 |
3 |
5 |
4 |
4 |
5 |
Easily repeatable |
2 |
2 |
1 |
2 |
5 |
4 |
4 |
||
10 |
Inexpensive |
2 |
2 |
1 |
3 |
5 |
3 |
1 |
||
Subtotal |
50 |
35 |
20 |
55 |
100 |
75 |
50 |
|||
Cost |
25 |
10 |
Capital investment |
4 |
2 |
x |
5 |
5 |
4 |
1 |
5 |
Labor |
4 |
4 |
2 |
4 |
5 |
4 |
4 |
||
5 |
Tooling |
3 |
2 |
1 |
4 |
4 |
3 |
1 |
||
5 |
Known Technology |
3 |
3 |
1 |
5 |
4 |
4 |
2 |
||
5 |
Maintenance required |
3 |
2 |
2 |
4 |
5 |
2 |
3 |
||
Subtotal |
105 |
75 |
xx |
135 |
140 |
105 |
60 |
|||
Safety |
25 |
10 |
Safe |
4 |
3 |
1 |
4 |
4 |
4 |
2 |
5 |
Ergonomic |
3 |
3 |
1 |
4 |
4 |
1 |
3 |
||
5 |
Clean |
4 |
3 |
1 |
4 |
5 |
3 |
1 |
||
Subtotal |
75 |
60 |
20 |
80 |
85 |
60 |
40 |
|||
Quality |
25 |
5 |
Skill required |
3 |
2 |
2 |
4 |
5 |
3 |
2 |
10 |
Meets customer need |
1 |
4 |
3 |
4 |
5 |
4 |
5 |
||
10 |
Defects per shifts |
2 |
3 |
1 |
4 |
5 |
4 |
5 |
||
Subtotal |
45 |
80 |
50 |
100 |
125 |
95 |
110 |
|||
Total |
227 |
217 |
xx |
317 |
355 |
263 |
214 |
From the table, the three best alternatives are chosen. In our example, the methods chosen are 5, 4, and 1. The three methods are test through simulation and the best one is implemented.
Presentation to the management is vital for Kaizen to succeed because it allows management to understand the effects of Kaizen project on the success of the firm. In addition, it provides an excellent platform for training the whole firm on Kaizen implementation. It is also used to provide feedback to enhance the implementation of Kaizen concept, leading to a culture of continuous improvement.