Key Definitions
1. MBWA � It refers to a management technique which involves a manager walking around in an unstructured way to check the status of the current work.
2. SMART goals � This are goals that are specific, measurable, attainable, realistic, and time-bound.
3. Sponsor � An organization or person that provides the fund for an activity or project to be carried out.
4. Facilitator � A person who engages in facilitation activities. Help people to understand their objectives.
Kaizen means continues improvement. Unlike the traditional western ideas of change, Kaizen requires little money, much common sense, and commitment from all workers and managers. It encourages small but continuous changes day after day.
The main aspect of Kaizen is that it is a continuous process � it does not end. Unlike the ordinary western method of scrapping everything and starting afresh, kaizen is a gradual and soft process.
Kaizen is best explained by developing an understanding of its 3 main aspects:
-
Gemba
-
Kaizen Blitz
-
Mini Kaizen.
1. Gemba
As told by Imani in his 1997 book titled "Gemba Kaizen", "The term "Gemba" was first used by Toyota in the 1950s when developing the famous Toyota Production System. It means walking to the real place where production is taking place."
However, the concept of Gemba remained unpopular until 1980 when Tom Peters popularized it in his book about management by wandering around (MBWA) titled "In Search of Excellence." Just like MBWA, Gemba walks take managers to the front lines to witness daily happenings in the workplace, but Gemba is more focused. It stresses the following;
-
In person observation of how work is done � this is the overruling principle of Gemba.
-
Value add-location � Walking to the actual work place and observing what's going on � as opposed to discussing workplace problems in a business meeting.
-
Teaming � Walking to the work place, and interacting with the employees in the true spirit of Kaizen � change for better.
The core principle behind Gemba is that for a manager to really understand a manufacturing process, he or she has to go to the actual spot where production is being done. Gemba is part of a bigger lean management philosophy popular as "3 Reals" which says. "You need to go the�
1. real place to observe the
2. real things to get the
3. real facts."
Objectives of a Gemba Walk
Normally, managers spend much of their time at their desks; gazing at their smartphones, reading reports, attending a meeting, and depending on their subordinates to bring them the latest information. Getting up and walking to the action center is a great opportunity for them to discover new things. It's an eye opener.
The aim of gemba walks isn't to map out your factory and record each area that needs improvement all at once. Gemba doesn't require one to search for errors and fix them immediately. Rather, the aim of a Gemba walk is to allow managers to walk out and see exactly what is happening, spark dialogue with workers, and then return to their office with ideas of some areas that might need improvement. Gemba walks allow managers to identify areas of waste that can be eliminated from the processes to enhance efficiency.
Gemba Walk � How to Do It
The secret to a successful walk is given by the difference between snooping and engagement. You are going to bring discontent if you are managing by walking around to see if your employees are really working. However, if your employees feel that you are genuinely interested in what they are doing, they will be looking forward to see you.
Therefore, during your gemba walks, approach your employees with interest, and respect for what they do. You should not try to correct behaviors or problems while you are out on the workstation. In fact, according to Fujio Cho, Toyota chairman, "You need to Go See, Ask Why, Show Respect and encourage creative thinking."
Go See
The aim is to understand Gemba (production area) from the viewpoints of people, process, and purpose. The question is, "Is the management working to align people and process to realize the set purpose?" Although purpose superficially comes first, when walking Gemba, you should concentrate first on the process. Begin by asking simple questions such as what your organization or employees are trying to achieve. Later you can begin your walk, observe, and ask questions with purpose in mind.
2. Ask Why
Having visited the workstations, it is time to analyze the process with the primary goal being to understand Gemba as a system. There are four lean lenses through which a workstation can be analyzed:
-
Solution view � it involves looking for opportunities to adopt lean tools (lean tools eradicate waste).
-
Waste view � it involves walking the workplace to identify waste.
-
Problem view � here, you need to begin with the workstation objectives and then focus on morale, delivery, quality, cost, and system in place to help attain the objectives. Are there rooms for improving the process of value creation?
� Kaizen view � seek forms, routines, tools, patterns.
3. Show Respect
Gemba-Kaizen dictates that managers must show respect to all stakeholders. Always look for signals of disrespect toward:
-
Employees � especially overburden or muri.
-
Customer � poor quality or poor delivery � especially from controllable fluctuation, mura or variations.
-
The organization itself � Look for problems and waste in the organization's processes.
The 4 Steps towards Gemba Success
There are four steps to realizing Gemba success. These are shown in the diagram below:
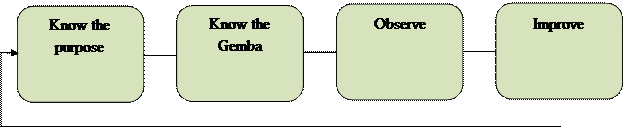
Note:
Step 1: Know the Purpose
Before you go out on your walk, you need to plan. Tackling a whole value creation system on a single walk is overwhelming and it gives rushed observations that are not only inaccurate, but also less useful.
Start by defining your business goals � both short-term and long-term � and throughout the walk, ask how each step contributes to the desired objectives.
Then, define the specific objectives of your gemba walk. For example, your goal could be to see whether there is over processing, unnecessary motion, or extra waiting in a certain process. Stay open-minded during the gemba walk, but remember that you can't observe everything in single walk,
Also, bear in mind that the primary objective of the walk is to dialogue with workers and to encourage them to be creative.
Step 2: Know the Gemba
To assess and observe Gemba, you need to understand it. Every business has several places where value creation takes place. Whatever locations your business operates in, know the exact standard procedures so that during the actual walk, you can gauge how effective they are and whether they should be changed. Bear in mind that you must think of your work location as a team asset. Calling a workplace your Gemba can really hinder your thinking and limit teamwork. Talk to employees about their process, not "your processes."
Step 3: Observe
During the gemba walk, give attention to aspects of the manufacturing process such as safety, housekeeping, and efficiency. You can also take a look at the waste pile to figure out the types of defects that are arising. Think about the purposes of your business, the people, and the manufacturing process. These three aspects are intertwined in that the purpose of your business � solving a customer problem � is attained through people who run the production process. If you note a problem, ask why and how it's arising, but do not try to correct or blame the employee. While at the gemba, focus on sparking a discussion and taking information. Consider the following questions:
-
What's working well?
-
Which processes add value?
-
Are standard procedures followed?
-
Are there deviations?
-
Is workplace tidiness a problem?
-
Is the planned output being achieved?
-
Are production machines in optimal performance conditions?
-
Is the production process safe?
-
Are there wastes of resources or time?
-
What individuals or workstation create value?
-
Are there defects?
-
Do workers need support or training?
Note that your gemba walk should be random so that workers will behave normally. With this in mind, you do want to make them feel comfortable and the best way to do this is to start a conversation with them. The following questions work best:
-
Would you mind showing me how to perform this task?
-
Is the task always done this way?
Step 4: Improve
After the walk, reflect on what you have seen. Then, come up with corrective measures, determine who will implement the changes, and follow-up to ensure the changes are actually implemented.
2. Kaizen Blitz
This is a quick improvement or change workshop designed to help generate results to distinct process problems within a few days. It is a method used by organizations to carry out planned process improvement or to solve business problems in a workshop setting, over a short timeframe.
The table below shows the specific benefits of a Kaizen Blitz over the conventional problem solving process:
Conventional process |
Kaizen Blitz |
Can take long � weeks or months |
Takes a few days |
Senior managers can lose interest |
High level of commitment by different parties |
Teams can lose momentum |
A focus on implementable and practical solutions |
Results take a long time to be realized. |
Results are normally quick. |
External facilitation or consultancy support can be expensive |
Improvement ideas normally come from the people working in the processes. |
Conventional organization process improvement plans can stretch out over many days, weeks or months while a Blitz takes just a few days.
Key Features of Kaizen Blitz
Normally, a kaizen blitz lasts for 5 days and it seeks to deliver defined performance improvements � but it can be shorter than 5 days. It requires all the right people to collaborate in analyzing the problem, developing improvement strategies, and implementing them. Noticeable benefits of the blitz start to emerge within the Blitz and are clearly identifiable within weeks after the blitz. In short, a kaizen blitz has the following features:
-
Is a focused 5 days event
-
Delivers specific performance
-
Participants include different people � for analyzing the problem, developing improvement solution, and for implementing the solution
-
Managers must commit to the resources and time required, and empower the Blitz team to accomplish the goal
-
Tangible outcomes are usually visible during the Blitz period and even after
Stages of Kaizen Blitz
A Kaizen Blitz goes through three main stages: Preparation, the Blitz Event, and Follow-up.
1. Preparation
The first stage involves:
-
Identifying a senior manager sponsor
-
Defining the improvement needed and scope of the process/problem to be addressed including setting SMART goals and identifying any constrain
-
Gathering available data as well as process information that will be required during the Blitz
-
Selecting and briefing the Blitz team
-
Briefing all other stakeholders
2. The Blitz Event
Here, we will look at a five day Blitz Event as an example to help you understand the event. See the table below;
Day |
Activities |
First day |
� Introduction by sponsor. � Process training and introductory Blitz. � Review and revising of Blitz plan definition (and high-level map). |
Second day |
� Process map as well as walk-through. � Identification of current issues (vs. the goals). � Initial data gathering. |
Third day |
� Continue data gathering (engage with clients and other stakeholders) � Analyze data � Develop initial views on viable solutions |
Fourth day |
� Prioritize and refine solutions for adoption � Begin adoption of solutions |
Fifth day |
� Prepare summary of solutions and analysis � Prepare plan for persistence of adoption as well as communications � Present results and recommendations to sponsor and other stakeholders |
3. Follow-up
In the last step, you need to:
-
Continue with adoption actions for processes not done during the five-days event.
-
Communicate process alterations to stakeholders.
-
Coach staff/manager and complete project hand-over to organization.
-
Measure benefits and impacts.
-
Sign-off achievements with sponsor.
3. Mini Kaizen
A Kaizen Blitz is a fast, big, and dramatic type of improvement but in the words of Norman Bodek, a teacher, author, publisher, and a consultant, "There is a Quicker and Easier Kaizen known as Mini Kaizen."
This form of Kaizen recognizes that the individual doing a certain project is the best person to come with improvement ideas � however small � that can improve efficiency of his or her job activity, the company process or job environment for that matter. Mini Kaizen encourages the workers to implement the changes since this can be attained with minimal time input on their side. Over time, these changes have a huge impact on the whole organization.
Mini Kaizen: Case Study 1
Dana Corporation, an American global supplier of sealing, thermal management and drive train technologies, has been using Mini Kaizen for over a decade. Management asks for twenty-four ideas every month from every worker and 80 percent are implemented.
Mini Kaizen: Case Study 2
Mini Kaizen is the missing element in many organizations but it is the core of Toyota production system. In 2009, Toyota stated that its employees are empowered with the ability to enhance their workplace through continuous improvement. This includes everything from safety and quality to productivity and maintenance of a conducive working environment. Suggestions and improvements by employees are the pillars of Toyota's success.
Mini Kaizen has a lot of benefits. For example, it empowers workers and improves their work experiences. Mini Kaizen enhances safety, quality, environments, cost structures, customer service, and throughput.
The Process of Mini Kaizen
The quickest and easiest Kaizen process works as shown:
1. The worker identifies a waste, problem, or an opportunity for change and notes it down.
2. The worker generates an improvement plan or idea and discusses it with the supervisor.
3. The supervisor reviews the plan within twenty-four hours and pushes for immediate action.
4. The worker adopts the plan. He or she takes leadership to adopt the plan.
5. The plan is noted down on a form in less than 3 minutes.
6. The supervisor posts the form to stimulate others and acknowledge the accomplishment.